Machinery
Modern, precise, flexible
Our modern machinery is built for precision, small to medium series and technically advanced tools in aluminum and plastic.
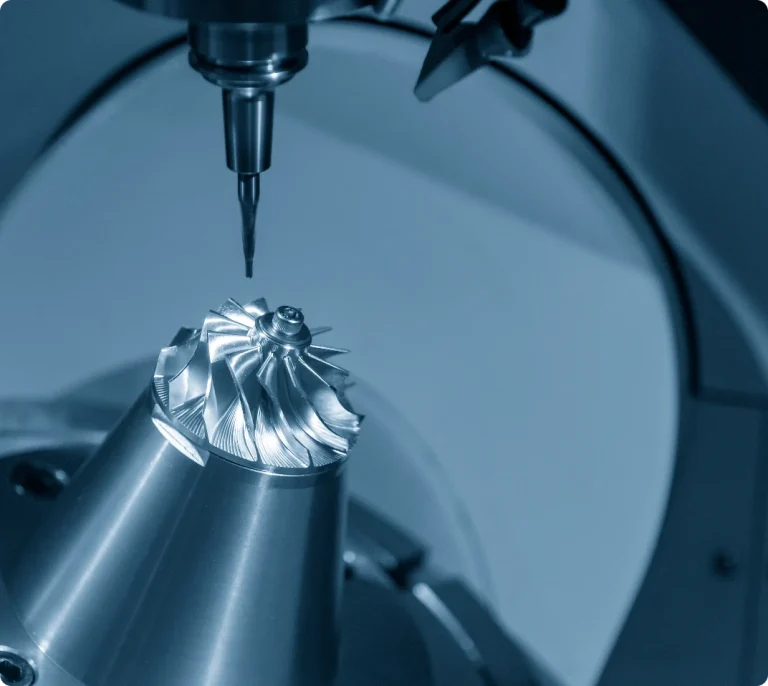
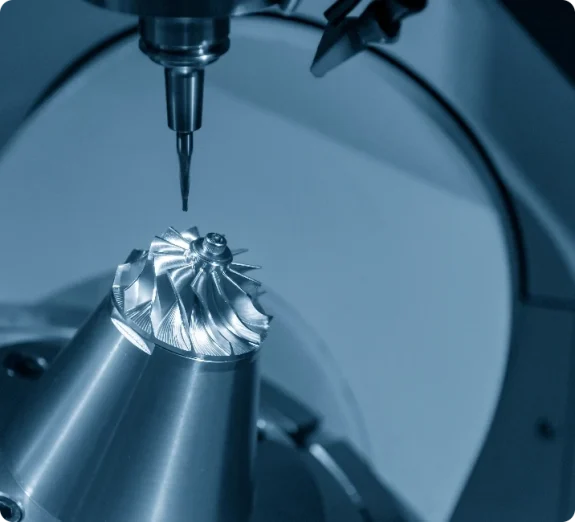
Full control and high quality
All our manufacturing takes place in our own workshop in Värnamo. By having all critical machines gathered internally, we ensure precision, speed and flexibility in every project. We can redirect capacity if necessary, respond quickly to adjustments and follow every detail throughout the process. This is true whether it's a new mold, subcontracting a major part or modifying a plastic mold.
Our machines are carefully selected to meet tough tolerance requirements, large workpieces and complex geometries. The combination of machines and skilled staff allows us to produce technically advanced tools with high quality and short lead times. The machinery is a crucial part of our offering as a new generation toolmaker.
Advanced machines for molds, parts and repairs
-
5-AXIAL MILLING
GROB G750
A horizontal 5-axis milling machine suitable for machining larger parts and almost all materials. It offers great versatility and high performance.
Working weight1500 kgArea of workX1000 Y1100 Z1175 Ø1280 -
5-AXIAL MILLING
GROB G550
A horizontal 5-axis milling machine adapted for larger parts and different materials, with high versatility and performance.
Working weight800 kgArea of workX800 Y1020 Z970 ⌀900 -
3-AXIAL MILLING
Micron VC1000
A Swiss 3-axis milling machine
Working weight800 kgArea of workX1000 Y560 Z700 -
SINKING GRID
AgieCharmille Form 30
A Swiss submerged spark machine
Working weight800 kgArea of workX600 Y400 Z400 -
WIRE ENGINEER
Fanuc 1D
CNC device made in Japan
Working weight800 kgArea of workX600 Y400 Z310 -
PLANSLIP
Plain solder
Grinds large flat surfaces
Working weight1000 kgArea of workX1000 Y600 Z400
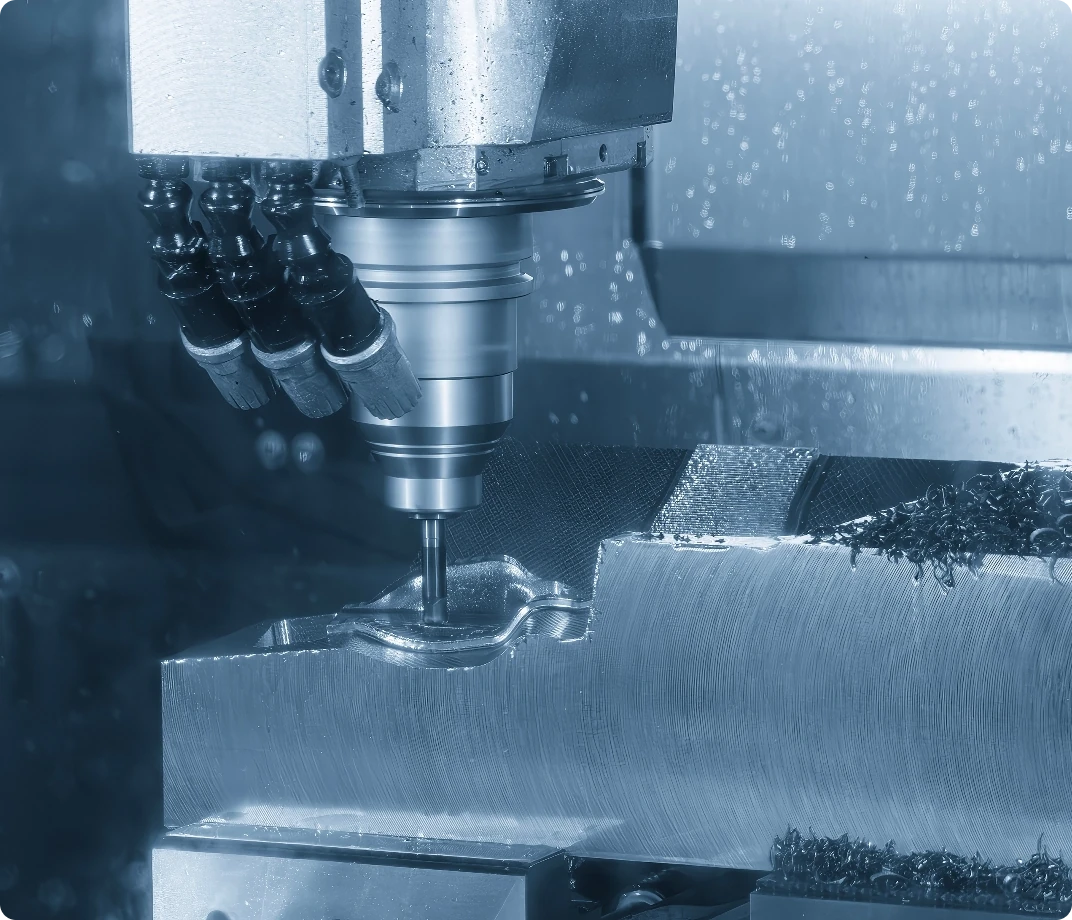
Different types of machines
-
5-axis milling machine
Our five-axis milling machines are used to machine large parts with complex geometries. The machines allow us to reach multiple surfaces in a single clamping, increasing precision and reducing lead times. Thanks to their high stability and flexibility, we can machine molds with tight tolerances and advanced structures, even in tougher materials. These machines are the heart of our tool production.
-
3-axis milling machine
Three-axis milling machines are mainly used for simpler geometries, plane machining and parts that require straight angles of attack. We use them for both contract parts and tooling parts, where machining requires stability and repeatability rather than simultaneous multi-axis motion. They are efficient, fast and an important part of our capacity for small to medium series.
-
Immersion spark
Recessed EDM is used when we need to process details where milling is not enough. With this method we can create sharp corners, deep holes and other details with very high precision in hard materials. The machine is particularly important in the manufacture of molds where precise inserts or cavities are required that cannot be milled mechanically.
-
Wire spark
Wire EDM is used to cut contours with very tight tolerances. It is particularly suitable for parts that require absolute accuracy of fit, such as cores or inserts for molds. By using wire that cuts with electrical discharge, we can create extremely precise shapes in materials where other machining would be difficult or impossible.
-
Planned slip
Surface grinding is used as a final step when we need perfectly flat surfaces with high surface finish. This is often crucial for fits between tool parts and sealing surfaces. The machine is also used in tool refurbishment and servicing where we restore worn surfaces to their original shape. This is a critical process for both new and existing components.
Precision at every stage through in-house production.
By having a complete range of machinery under one roof, we can offer both breadth and depth in our manufacturing. All stages take place in direct contact with our designers and technicians, which minimizes the risk of misunderstandings and ensures that every detail meets the requirements.
Our machinery makes it possible to take responsibility for the entire chain, from raw material to finished component, including service and adjustments. For you as a customer, this means shorter lead times, better quality and a partner who is always ready to deliver, even when conditions change.
Contact us